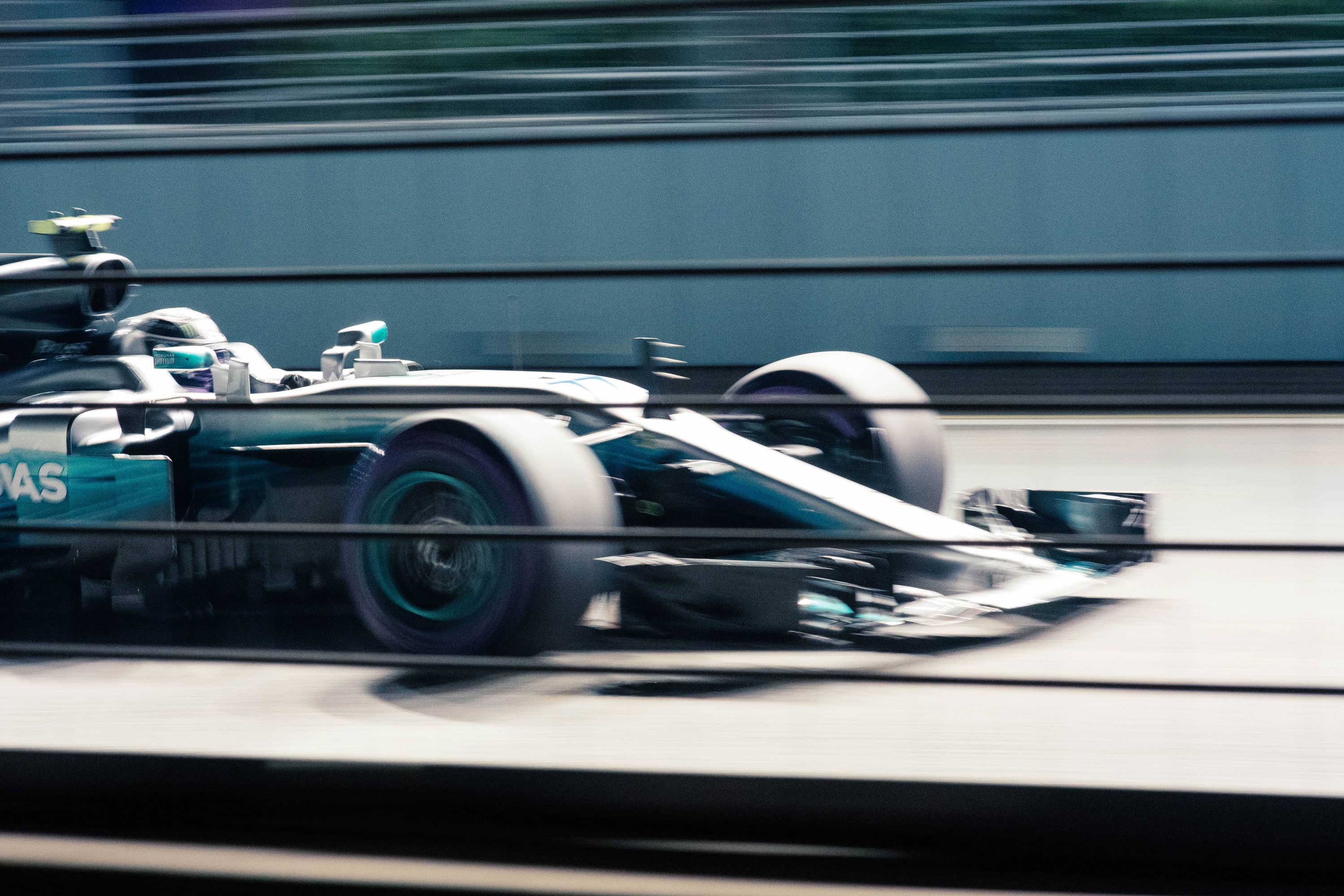
You brake, you lose.
The German valve industry knows this wisdom and therefore keeps up the pace in the further development of its companies.
Friction, wear and lubrication
Technology on the podium
The result is, among other things, sustained technology leadership even among smaller manufacturers of industrial valves. In many application areas, they stand on the podium at the award ceremony, only to quickly resume their course of innovation afterwards.
The trade association supports this objective of continuous product optimization with its initiatives for joint industrial research. In this way, it helps to overcome resource barriers and strengthen the competitiveness of its predominantly medium-sized member companies.
The surfaces of a valve are one of the classic fields of research in the valve industry. The aim is to increase their resistance – both internally and externally – to influences of all kinds. However, solutions for surface treatments to improve tribological properties are often expensive, especially in relation to the relatively small surfaces in valve construction. They usually require complex pre- and post-treatment of the components. In addition, surface treatments often influence the chemical resistance of the surfaces and thus limit the application use.
Competent racing team
The VDMA joint research project “Thermally sprayed coatings for valve construction”, which has now been completed, was conducted in this context. In this project with RWTH Aachen and TU Darmstadt, new coatings were developed that are suitable for a wide range of loads in valve construction. By integrating solid lubricants, the wear and friction behavior in particular was significantly improved. For example, by integrating hexagonal boron nitride in specially developed WC/CoCr coatings, the coefficient of friction was reduced by 30 percent compared with solid-lubricant-free coatings. In addition, a reduction in the wear coefficient of around 75 percent was achieved.
In aggressive media such as hydrochloric acid, however, solid lubricants and coating irregularities such as pores are known to be critical, as the medium more easily enters the coating, where undercorrosion is initiated. By using a new ultra-high velocity flame spraying process and a finer particle fraction, it was possible to achieve a sufficiently dense microstructure that remains resistant even in aggressive media.

Staying on track for success
The follow-up project “Low-finish fine powder coatings for corrosion and wear protection in valve construction” is now intended to advance the development of near-net-shape coatings for valve components in order to reduce or even eliminate cost-intensive grinding finishing steps (e.g. grinding, lapping).
Here, too, the ultimate aim is to achieve an additional reduction in friction losses and wear, resulting in lower energy and process costs for users and thus ultimately improving the competitiveness of valve manufacturers.
The use of high velocity flame spraying process variants specially adapted for valve components and the associated demonstrator tests should increase the acceptance of the coatings by valve manufacturers and users and thus ensure rapid transfer to the valve industry.
The checkered flag waves to the best ...
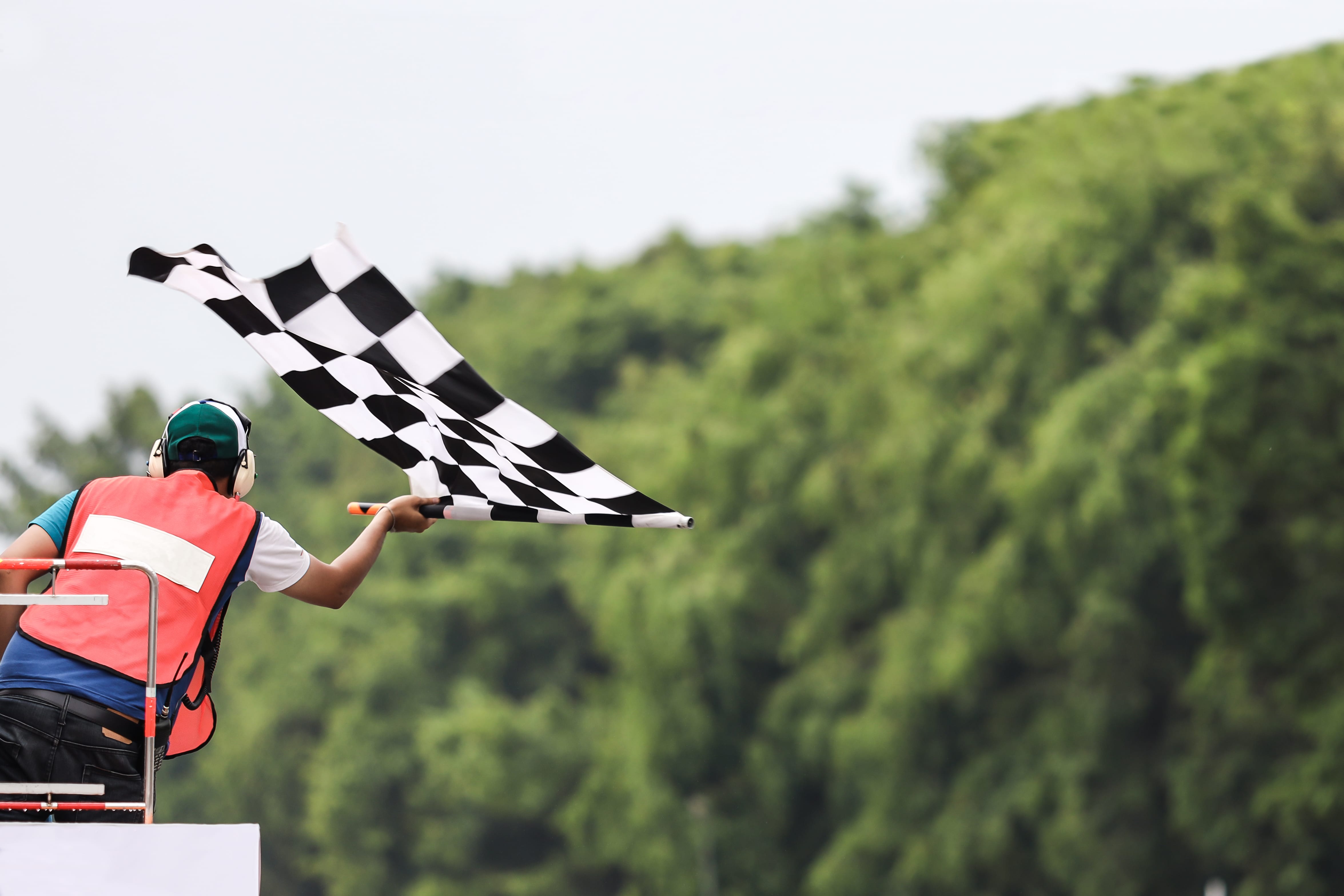
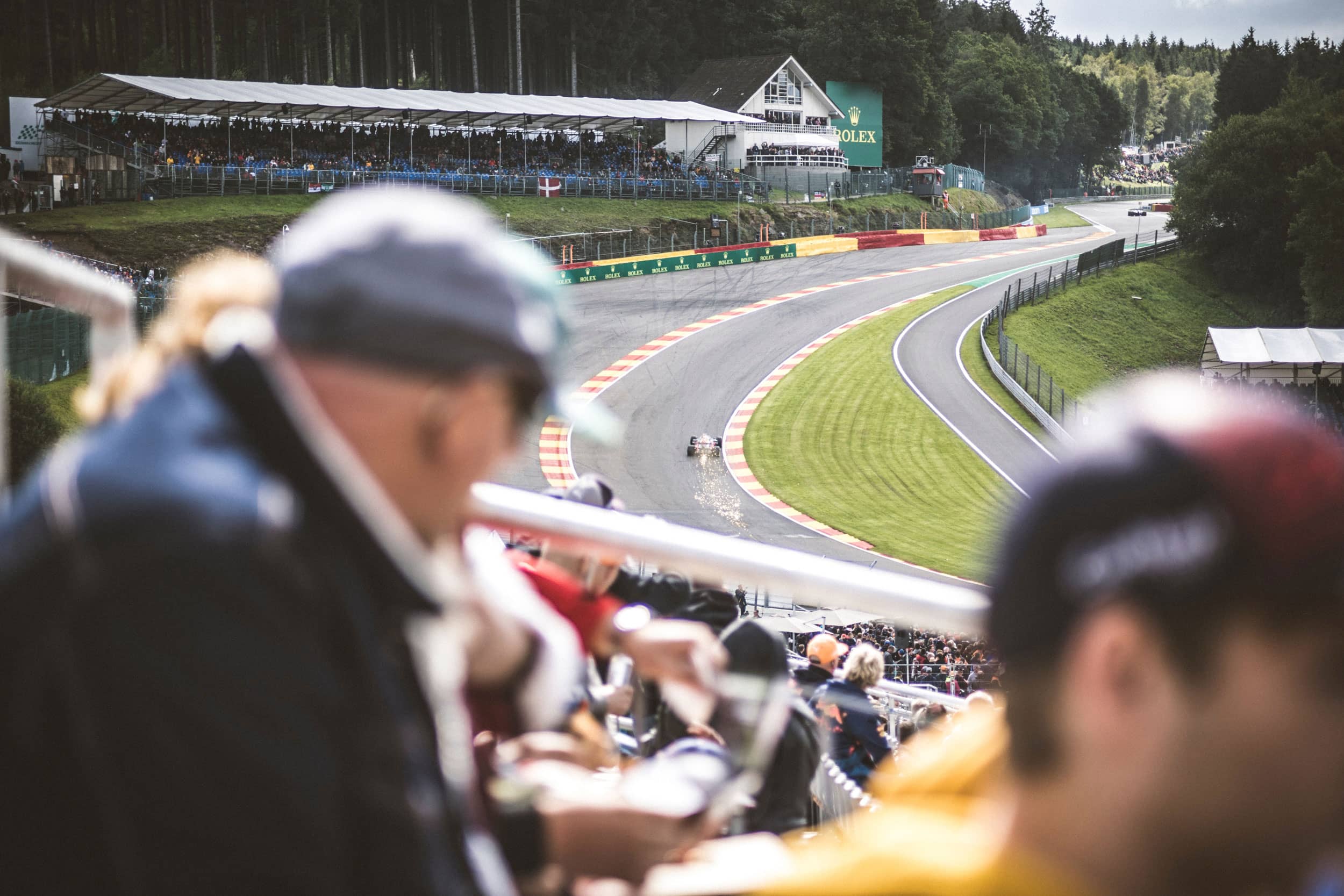
... when they participate in the race.
Target flag in sight?
On this occasion, the project knowledge gained and the process parameters determined for the demonstrator coatings could also create the basis for the participating valve manufacturers, in cooperation with powder manufacturers and, if necessary, contract coaters, to master the very demanding handling of highly developed ultra-fine powders during thermal spraying, in order to bring appropriate coatings onto the market independently and in a timely manner.
That would give them a technological lead. Once again, they would be the first to take the checkered flag.
Conclusion: If you’re not there, you’ll lose out! Similar to braking.